Getreu seiner Markenessenz beschreitet Alpine immer wieder neue Wege. Um sich der Herausforderung der Dekarbonisierung zu stellen, leistet der Automobilhersteller Pionierarbeit und verwendet für einige Teile des vollelektrischen Prototypen Alpine A110 E-ternité Leinen anstelle von Karbon.
Flachs, der Rohstoff für das natürliche und leichte Material, findet sich ganz in der Nähe des Stammwerks Dieppe in der Normandie. Florent, Exterior Accessory Design Leader, und David, Head of Upstream Workflows, zwei Entwickler aus dem ALP’INNOV CENTER – machten dies möglich. Hier geben sie einen Einblick in die Erfolgsgeschichte. Alpine beweist einmal mehr seine Innovationskraft. Das Unternehmen treibt die Senkung der Kohlenstoffemissionen zur Schonung der Umwelt voran, verringert das Gewicht seiner Autos und setzt auf nachhaltige Rohstoffe. Der vollelektrische Prototyp Alpine A110 E-ternité, der im Juli 2022 beim Großen Preis von Frankreich debütierte, ist das perfekte Beispiel dafür.
„Es war eine technische Herausforderung, von einer konventionellen A110 mit Verbrennungsmotor auf die vollelektrische A110 E-ternité umzustellen. Der umweltbewusste Ansatz, Leinen in einem Fahrzeug zu verwenden, ist eine echte Chance für uns. Das Material ist leichter und markiert sowohl technologisch als auch ökologisch ein Schritt nach vorn.“
Florent, Exterior Accessory Design Leader bei Alpine
Flachs eröffnet neue Möglichkeiten
Die Alpine A110 E-ternité ermöglicht es Alpine, Innovationen zu testen, die künftig in den Modellen der Alpine Dream Garage zu finden sein werden. Das Modell ist wendig wie jedes Alpine Fahrzeug und dabei mit 1.378 Kilogramm leichter als jedes andere Elektromodell in seinem Segment. Und dies trotz der 392 Kilogramm schweren Batterien. Ein Grund dafür: Fronthaube, Dach, Heckabdeckung, Sitzschalen und Heckschürze bestehen aus Leinen. Florent und David haben diese kohlenstoffarmen Karosserieteile entwickelt, um den Weg in die Zukunft der Marke zu ebnen. Das Material ist natürlich, stammt aus biologischem Anbau, und sein Herstellungsprozess ist weit weniger energieintensiv als der von Karbon – dem Material der Wahl, um das Gewicht eines Sportwagens zu senken. Die geringe Dichte und damit das geringe Gewicht, die Widerstandsfähigkeit und die akustischen Eigenschaften sind weitere Pluspunkte, die für Leinen sprechen. Das verwendete Material stammt von Terre de Lin, dem weltweit führenden Unternehmen in der Flachsproduktion mit Produktion in der Nähe von Dieppe, dem Geburtsort der Marke Alpine und Sitz der Manufacture Alpine Dieppe Jean Rédélé.
Der Weg des Leinens
Um zu wachsen, braucht Flachs Erde, Wasser und Sonne. Doch bevor die zu Leinen gewobenen Fasern das Labor von Alpine erreichen, werden sie von Terre de Lin auf verschiedene Weise verarbeitet. Im März und April erfolgt die Aussaat, zu Beginn des Sommers werden die Pflanzen geerntet. Auf den Feldern in Reihen angeordnet, verrotten die Pflanzen – ein natürlicher Prozess, der die Flachsfasern von den Holzstängeln löst. Anschließend werden die langen Fasern gekämmt, geglättet, zu Garn gestreckt und zu 45 Kilogramm schweren Ballen gebündelt. In der Spinnerei wird das Material zu Stoff gewoben und anschließend an Alpine geliefert.
Doch wie wird daraus eine Motorhaube, eine Sitzschale oder ein Dach? Das Alpine Labor in Les Ulis, südwestlich von Paris, kombiniert das getrocknete Gewebe mit Baumwollgarn und webt daraus ein biaxiales (45-Grad) Muster. Der zu 95 Prozent aus Leinen und zu fünf Prozent aus Baumwolle bestehende Stoff wird anschließend in Epoxidharz getränkt und anschließend in Form gelegt.
Dabei achten die Mitarbeiter sorgfältig auf die Ausrichtung des Gewebes sowie die Anzahl der Falten und bringen die äußere, sichtbare Oberfläche mit der Form in Kontakt. Im nächsten Schritt wird das Teil abgedeckt und vakuumbehandelt. Danach wird das Musterteil aus der Form genommen, von Hand zugeschnitten und im ALP’INNOV CENTER montiert.
Forschung im Zeichen der Leistung
Ähnlich wie der Leinenrumpf-Katamaran des Segelprofis Roland Jourdain sind die innovativen Autos von Alpine auf Leistung ausgelegt. Terre de Lin liefert übrigens das Rohmaterial für beide Hersteller. „Mit der Zeit wollen wir auch das Epoxidharz austauschen, um die Bauteile komplett zu dekarbonisieren“, sagt Florent. Er und David sind auf der Suche nach Harzen aus biologischem Anbau, die ihren Anforderungen entsprechen. Dieses unermüdliche Streben nach Verbesserung ist ein Beispiel dafür, wie Ernst es Alpine mit der Performance-Steigerung ist.
Die Karbon-Fronthaube einer Alpine A110 R wiegt 3,98 Kilogramm, die serienmäßige A110 Aluminium-Motorhaube 6,9 Kilogramm. Ein aus Leinen gefertigtes Teil wiegt aktuell jedoch noch 20 Prozent mehr als ein Karbonelement. Mit ihrem Wissen über Verbundwerkstoffe können die beiden Entwickler jedoch eine große Anzahl von Funktionen integrieren und die Anzahl der Teile reduzieren. Florent sagt, dass alle Optionen auf dem Tisch liegen. Sogar die Entwicklung von Leinenformen für die Fertigung ziehen sie ernsthaft in Betracht.
„Wir denken darüber nach, in Zukunft Teile aus Kohlefaser, Glas oder Leinen in derselben Form herzustellen. Noch ist es zu früh, um über den Einsatz von Leinen in der Serie im großen Maßstab bei Alpine zu sprechen – aber die ersten Versuche sehen vielversprechend aus.“
Florent, Exterior Accessory Design Leader bei Alpine
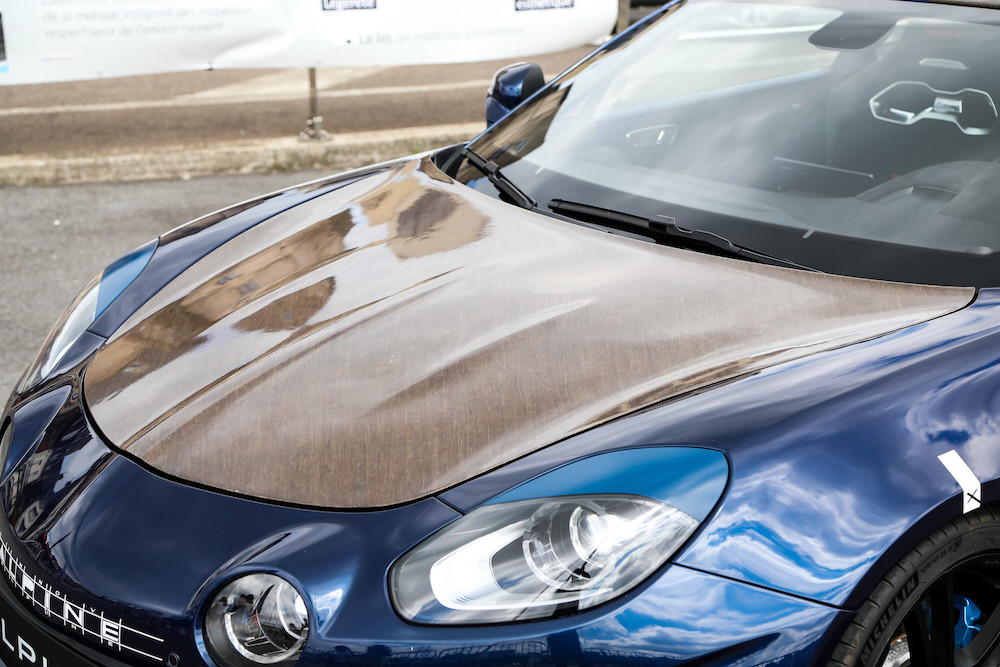
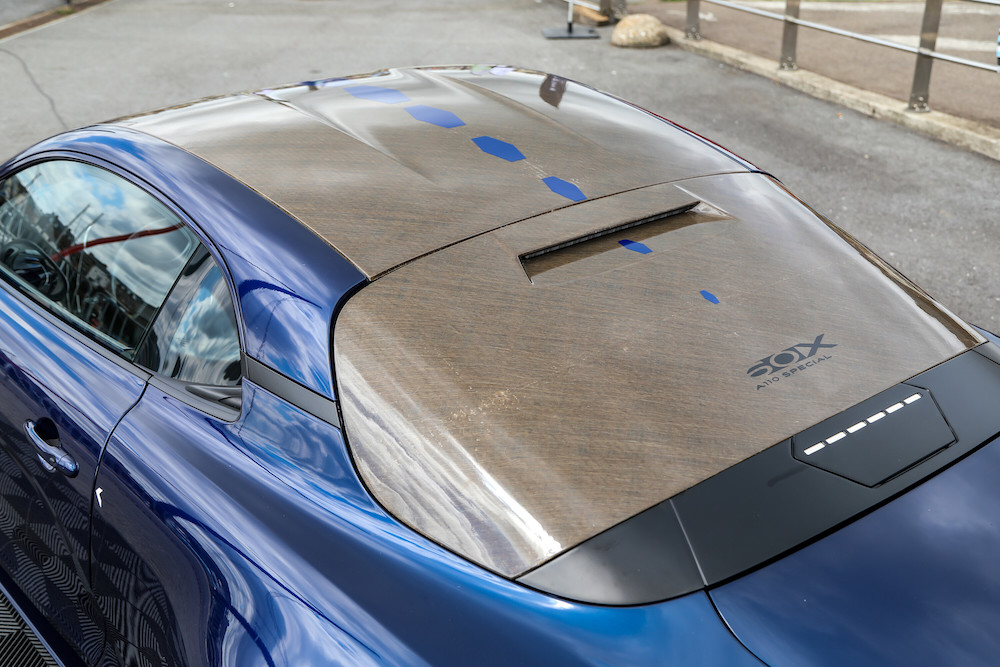

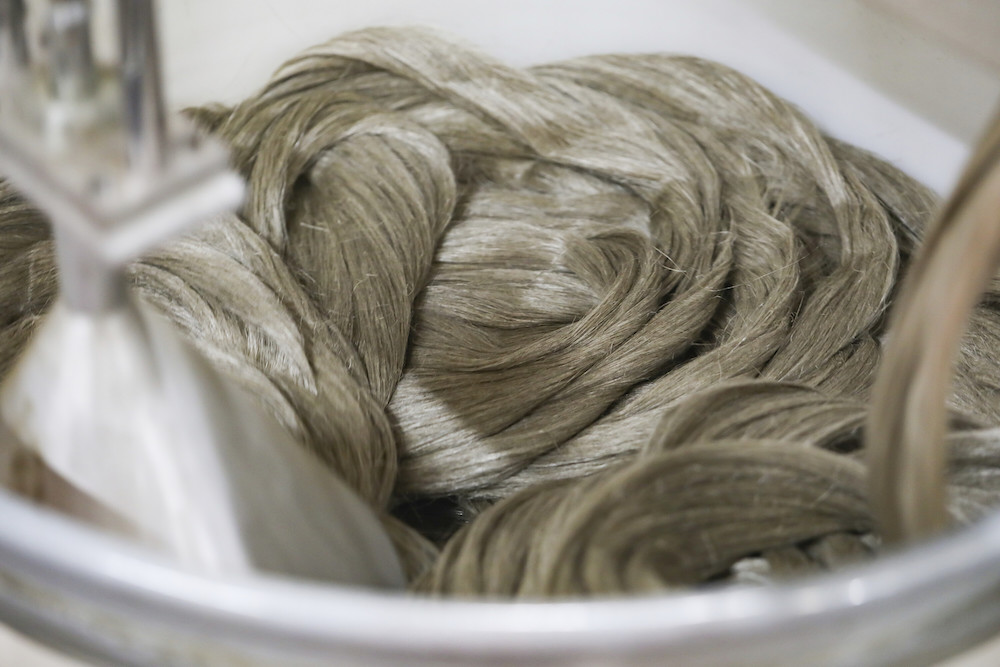